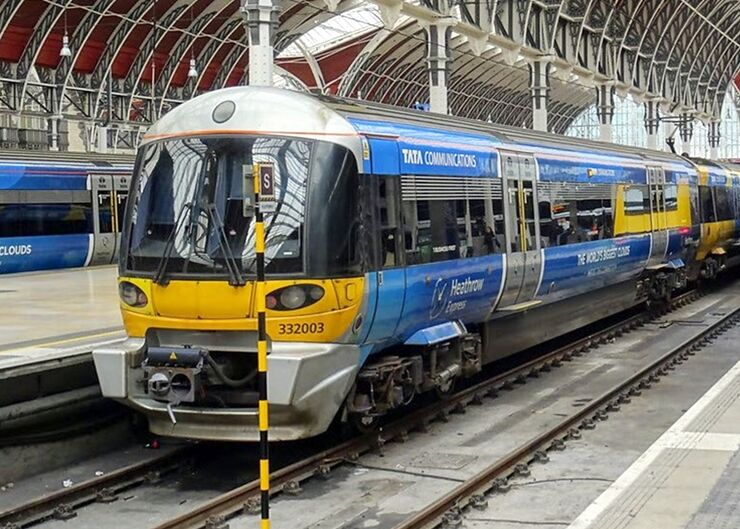
This project was discussed in detail in a webinar as part of NEC's 30th anniversary - read on below, or watch the recording here.
The original 6.8 km tunneled section of the Heathrow Express rail link in London, UK was the first major project to be procured using The New Engineering Contract (NEC). This was the 1993 first edition of what went on to become the NEC4 suite of contracts now in use worldwide.
Client British Airports Authority (BAA), now Heathrow Airport Holdings Limited , took the pioneering step of adopting the new collaborative-style contract for its express rail link to Paddington Station in a bid to improve cost and programme control. At the time, around a third of its construction projects were being delivered late or over budget.
This pioneering approach was championed by David Williams, then BAA group construction director and the NEC Users’ Group’s first chairman, from 1994 to 1997. BAA as a business wanted greater certainty of outcome for their contracts, which on average overran by 30% and increased in cost by 30%. NEC was seen as a way to improve this performance.
The Heathrow Express project involved building a new grade-separated junction with the existing Great Western mainline, which was linked via a cutting and two 3.6 km long 5.6 m internal diameter running tunnels crossing under the M4 motorway to a new 200 m long, triple-bore underground station in Heathrow’s central terminal area (now called Heathrow Terminals 2 & 3). It also included a 2.8 km extension tunnel to a new 200 m long, twin-bore station at Terminal 4, eight escape and ventilation shafts, and electrification of the 20 km stretch of mainline into Paddington.
BAA awarded a £62 million NEC Option A (priced contract with activity schedule) to Balfour Beatty for the tunneling and shaft works, and construction started in February 1994. In addition to using NEC, BAA had also decided to pioneer the relatively new sprayed concrete lining (SCL) method for digging and lining the turnouts, crossovers and 9 m wide station tunnels in London Clay. Unfortunately a major collapse of the part-built SCL central station tunnels occurred on the morning of the 21 October 1994 and, while no-one was injured, there was significant pavement and isolated building damage in the central terminal area (Finch, 1997).
Rather than resort to protracted and expensive litigation, the project team and Balfour Beatty worked collaboratively to resolve the issue in the most cost-effective way possible. This involved rapidly filling the tunnels with foamed concrete then building a 60 m diameter, 30 m deep cofferdam around the collapse area, which provided some construction benefits and opportunities to BAA (Hill and Harrison, 1999). The total additional cost came to £150 million, shared between BAA and Balfour Beatty, and the project was completed only six months later than originally planned. This remarkable recovery is a testament to the parties working in an integrated team and the NEC processes were a contributing factor to the recovery.
In June 1998 non-stop Heathrow Express trains started delivering passengers and their checked-in luggage to Heathrow Central and Terminal 4 in a record journey time of just 15 minutes. The rail link was extended to Terminal 5 ten years later. Since 2018, the Heathrow Express service has been jointly operated by Great Western Railway and Heathrow Express Operating Company, a subsidiary of Heathrow Airport Holdings. Its fleet of electrical multiple unit trains was replaced in 2020 and they continue to run every 15 minutes to Terminals 2&3 and Terminal 5, carrying an average of 17,000 passengers a day.
Radical new contract
BAA’s then project manager Gren Tipper, now operations director with Construction Clients' Leadership Group, and NEC consultant Barry Trebes, then working with BAA as a quantity surveyor for Needlemans, recall their experiences of working on the project in an NEC webinar celebrating NEC’s 30th anniversary (NEC, 2023).
Tipper confirms the decision to try the radical new NEC contract was driven by BAA group construction director David Williams. ‘David was adamant about sorting out BAA’s delivery of projects as about 30% of them were over time and over budget. He was quite revolutionary, introducing construction management long before anyone else did it in the UK and embracing design and build where appropriate. For me he was one of the most inspirational directors in BAA and probably in the industry.’
Williams initially arranged for BAA to trial NEC on a new terminal at Southampton airport in 1993 before adopting it that same year for the challenging Heathrow Express tunnels. Tipper recalls that using NEC was a daunting prospect. ‘It was a new contract and we had never used it before, so there was a degree of nervousness. But once we got started it seemed a most natural way to manage the project and everything slipped into place quite readily’.
Trebes remembers at the end of 1992 being halfway through preparing bills of quantities for the project under the ICE Conditions of Contract when BAA decide to switch to NEC. ‘It was a bold and very different change given we were a long way down producing traditional contract documents. But BAA were always looking to improve the way they did things and I learned so much from working with them, in particular David Williams.’
Tunnelling challenges
Tipper says it was a challenging project from the outset. ‘In addition to having to build a 100 m long SCL trial tunnel near Terminal 4 in 1992 (Dean and Bassett, 1995), in 1993 the ground surveys found a massive pool of aviation fuel floating on top of the groundwater in the central terminal area. This had to be pumped out as part of the enabling works. During tunnelling works in 1994 we found via the ground survey that a lot of the clay in the Stockley Park area had been excavated for brickmaking and backfilled with domestic refuse, which we also had to remove.’
Then, with the tunnels around 30% complete, Tipper was woken at 12.30 am on 21 October 1994 to be told about the extensive ground movements in the central terminal area as the part-built SCL tunnel linings started to fail at their construction joints some 26 m below ground. ‘The tunnels continued to fail over two more days, causing three surface craters and settlements of 0.2 to 2 m locally over the collapse area. The failure initially brought chaos to the heart of the airport but fortunately no-one was injured.’
Trebes says prompt collaborative action was taken to drill down to the tunnels. ‘We pumped in about 20,000 m3 of foamed concrete, which covered everything left in the tunnels, from Hydrema excavators to welding gas bottles. We had round-the-clock concrete deliveries from all over London’.
Switch to single team
He says the major change that followed was a decision to start working as a single team to recover and complete the project. ‘It was such a big learning experience for everyone when we realised how much more efficient and effective it was to work as an integrated team. For the first time we were sitting and working directly alongside the client and all its commercial, design and delivery teams, sharing and discussing solutions and changes collaboratively, and keeping proper records.’
Trebes adds that a major commercial benefit of using NEC was that at the time of the collapse and going forward, the budget and programme were up to date. ‘Through the NEC contract management processes we always knew where we were on costs through agreed compensation events and we kept on top of the programme. We were far more informed when the incident happened than if we had been working on a traditional contract, which put us in a much better position to recover the situation’.
Tipper says BAA’s then chief executive Sir John Egan, who went on to publish his seminal report Rethinking Construction (Egan, 1998) was an inspiration to the project team. ‘He put blame completely to one side, met Balfour Beatty at the highest level and paved the way forward for us to all work together. Once we got the tunnels back under control, he said the only way we could deal with this was if we entered a relationship where we both knew it was win-win.
‘It was therefore agreed that after taking account of insurance cover and scope benefits resulting in more usable space from building the recovery cofferdam, the parties would share the remaining additional costs of completing the project. This was the best recipe for collaboration as there were no distractions centred around time versus cost to complete at pace.’
Learning process
He says it was huge learning process for everyone involved. ‘Although the project team had been executing the contract in the spirit of NEC, sharing financial loss really showed us what collaboration and partnering looked like. A key learning point was that the closer you can work together on the pain-gain share, where you are both equally motivated to get it right, the better the end result’.
Trebes says the contract management processes in NEC, which was switched to an option E cost-reimbursable contract, came into play significantly once the recovery started. ‘In the first nine months we had something like 2000 contract communications, including early warnings and compensation event notifications and quotations. It was hard work keeping on top of the all the communications, keeping on top of change and keeping on top of the programme, but we had a lot of invaluable support and guidance from regular contact with NEC’s creator Martin Barnes’.
He concludes, ‘NEC certainly provided an effective tool with good management processes to help us through this challenging project. At the time of the collapse, we were in a good situation to understand where we were commercially and, while we initially found it difficult to work as a single integrated team after the collapse, we soon realised it was what NEC was driving us towards anyway. The contract promoted talking to each other, working together, discussing things and consulting with each other so that you make the most informed decisions with the best information. It is a something I have never forgotten.’
Benefits of using NEC
- NEC contract management mechanisms ensured the project team was up to date with budget and programme prior to the central station tunnel collapse, putting them in a better position to recover the situation than a traditional contract would have done.
- NEC early warning and compensation event processes came into play significantly once the complex recovery work started, enabling the project team to keep on top of the fast-changing budget and programme.
- NEC facilitated the then radical decision to switch to working as a single integrated team, encouraging true collaboration and partnering to minimise shared losses and complete the project just six months later than originally planned.
References
- Deane A and Bassett R (1995) The Heathrow Express Trial Tunnel Proceedings of the Institution of Civil Engineers - Geotechnical Engineering 1995 113:3, 144−156.
- Egan J (1998) Rethinking Construction, Report of the Construction Task Force, HMSO: London.
- Finch A (1997) Heathrow Express Recovery from Adversity, Going Underground 1997, 97−111, Thomas Telford: London.
- Hill I and Harrison D (1999) The Heathrow Express: structural design of the Central Terminal Area station. Proceedings of the Institution of Civil Engineers – Structures and Buildings 1999 134:1, 87−95
- NEC (2023) NEC30 Webinar: Heathrow Express – from disaster to success and how NEC helped