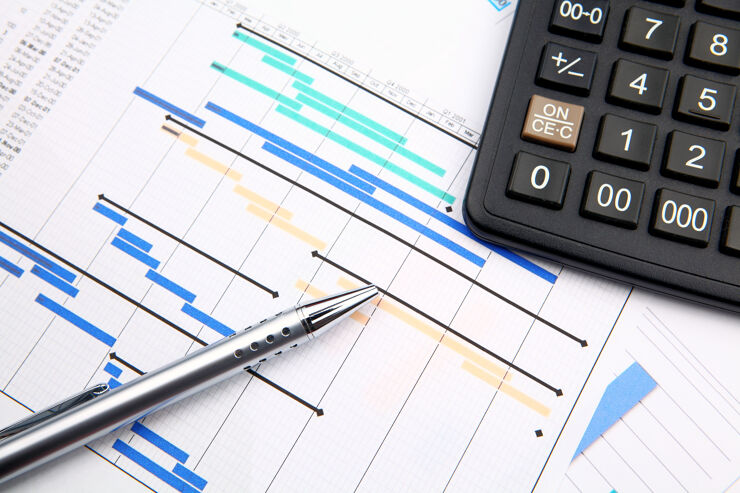
Key Points
- NEC4 ECC Option C and E contracts allow the project manager to check the contractor’s records that ultimately support defined cost payments.
- NEC4 ECC contracts define what can be charged as equipment based on different scenarios shown in the schedule of cost components.
- This article provides guidance on what to look for when auditing equipment costs on NEC4 Option C and E contracts.
The NEC4 Engineering and Construction Contract (ECC) Option C (target contract with activity schedule) and E (cost reimbursable contract) are commonly used for procuring high-risk infrastructure projects in the UK. The basic clauses allow project managers to inspect accounts and records of their choice in relation to defined cost items claimed.
In issue 129 I provided guidance on the audit of directly employed staff costs (Ward 2024a) and in issue 131 we covered labour agency costs (Ward 2024b). This article looks at equipment costs. NEC terminology differs from that of the wider industry where the term ‘plant’ is used.
Definitions
In NEC terms, equipment refers specifically to items used by the contractor to provide the works, whereas plant and materials are intended to be incorporated into the works themselves.
NEC4 ECC contracts define what can be charged as equipment based on different scenarios shown in the schedule of cost components. Typically, these include equipment that is listed in the contract data, owned by the contractor, hired from a group company or cross-hired from third-party plant-hire suppliers. There is also the proviso that it is used within the working areas. Which scenario applies will be determined by the contractor’s procurement and asset management strategy. There will also be certain projects which require the sourcing of special equipment, which will need referencing in the contract data.
Before reviewing equipment costs, NEC4 auditors should check if an initial equipment budget and resource plan exist to understand expected equipment types, durations and supply sources. Demonstrating equipment costs can be complex due to it often being represented via numerous low-value transactions. Effective data visualisation is therefore essential.
For third-party equipment, auditors should expect accounts and records documentation to be based on purchase orders, hire terms, invoices and payment proof. For contractor-owned equipment costs, auditors should expect benchmarking to show market rates (core clause 52.1). Additional records, as outlined in the scope (core clause 52.2), may include monthly plant reports with utilisation data and site records confirming equipment needs and timings.
Read the contract
Equipment is one of the few cost components that does not get heavily amended, but auditors should still check the contract in all the usual places (schedule of cost components, Z clauses and scope information) for potential amendments.
Under the standard schedule of cost components, third-party equipment should have traditional invoices while contractor-owned equipment should show either an internal charge rate (via an established internal price list) or inter-company invoice. These costs should align with market rates for value for money assurance.
There may also be equipment bought specifically for the project. If so, it should be listed in the contract data with the contract charge being the effective diminution of value, whether sold after use or assessed at its post-project market value.
There is also special equipment, which needs to be listed in contract data too. It has a value in use but cannot easily be supported by accounting records. A reason for this might be the rarity or age of the item, such as a specific size of tower crane.
Auditors should carefully review contract rules on equipment cost management, including requirements for hire versus buy decisions, utilisation data, monthly plans, condition reports and budget analysis with variance explanations. These principles also apply to equipment on key reimbursable subcontract packages, especially if contract terms flow down the supply chain.
Understand the environment
Auditors should understand the importance of how equipment costs are prepared, controlled and reported in the project as this heavily influences mischarging risk. They should do the following:
- Understand the project context: visit the site, equipment yard, and speak with the equipment manager to understand equipment handling, inspection and daily management.
- Explore data sources: identify any additional equipment data beyond the basic cost ledger.
- Assess equipment allocation: check if the contractor is sharing equipment across projects, posing a risk of duplicate charges.
- Review equipment account: evaluate the progression and review history of the equipment account. Confirm any idle periods, withheld or disallowed costs (clause 11.2 (26)) and the contractor’s response.
- Check for embedded costs: ensure equipment is not included in other rates, such as vehicles or information technology included in pre-agreed people rates.
- Understand audit scope: clarify if your audit supports routine application-for-payment assessments or has final assessment implications (clause 50.9).
Visualise data and design tests
Equipment data is often the most challenging cost ledger dataset to interpret and sample, making the above guidance crucial for understanding the hiring process and identifying additional data and reports to understand and clarify equipment charges.
With a solid dataset, including accounting and site records, equipment analysis can cover fields like supplier, type, units and rates. Auditors should start by tackling data volume with a simple monthly spend graph. This should align with core labour activity, showing peaks with high-use equipment, such as earth movers, and lower spend at the start and end phases. Further breakdowns by equipment type reveal major cost areas, which are essential for market rate checks.
Analysing one busy month can highlight repetitive charge patterns. For example, in a recent review of 5,000 transactions, a few quick graphs identified only 35 large assets that made up most of the costs. Smaller items generated high entry volumes but minimal cost impact, allowing for a focused inspection on key assets.
Further data analysis for equipment is possible, including the following:
- Spend per supplier, which is useful for assessing rebate potential and use of internal companies
- Spend versus budget at a work breakdown structure
- Spend per asset type and lower-level description, such as hire, transport, maintenance and damage
- Aged equipment accruals if accounting system picks up initial liabilities before invoice matching
- Operated equipment hire misaligned to labour hire or cost
- Operated equipment hire during site closures
- Operated equipment cost versus telematics usage
- Retrospective hire versus buy analysis
- Frequency of equipment booking, such as high or low hours and overtime patterns
Adding site records such as allocation sheets, site diaries, telematics and cabin closed-circuit television can quickly verify the necessity, accuracy and value for money of larger assets used on the project. Figures 1 and 2 are examples of simple graphs which show what analysis is possible.
A thorough understanding of the environment, plus good data analysis should help shape where costs may be mis-charged against the identified rules. It is important to consider or link all the rules back to specific tests. This should identify individual equipment items or trends and patterns of interest for further inspection.
Evaluate records and report
Auditors should design a practical sampling strategy for risk-based and key transactions, ensuring adequate assurance coverage. They should focus on high-risk assets and scenarios, such as contract compliance for special equipment and verifying damaged equipment costs against hire conditions and contract rules.
Auditors should concentrate core testing on major third-party and internal hires, keeping sampling manageable and representative of the broader dataset. Request records, review thoroughly and, if issues arise, investigate root causes, considering whether broader sampling may be needed to understand any control weaknesses or isolated errors.
Finally, auditors should document the work thoroughly as others may need to access it later. Too often, equipment reviews conclude as ‘all OK’ with little recorded detail. At best, partial reconciliations between cost ledgers and hire reports are noted, often dismissed as too complex due to data volume.
References
Ward D (2024a) Assuring staff costs on NEC4 Option C and E contracts. NEC Newsletter 129 (January 2024): 9–10.
Ward D (2024b) Assuring labour and agency costs on NEC4 Option C and E contracts. NEC Newsletter 131 (May 2024): 9–10.