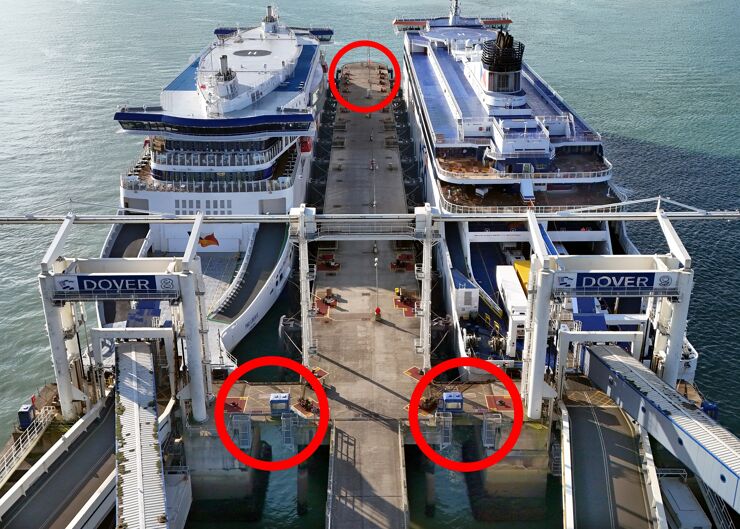
NEC has been used to deliver a small but critically important upgrade at the Port of Dover, the UK’s busiest international roll-on-roll-of (ro-ro) ferry port. The port engaged VolkerLaser to replace the life-expired elastomeric and uni-guide bearings of four of its pier F bridge structures under an NEC3 Engineering and Construction Contract (ECC) Option A (priced contract with activity schedule). The £1.3 million works started in October 2022 and were completed on programme and budget in June 2023.
Built in 2005, pier F in the eastern docks provides the port’s strategically important ro-ro berths 8 and 9. Together with four other ro-ro berths, these handle up to 260 km of freight traffic per day, facilitating up to £144 billion or one third of the UK’s trade in goods with the EU each year. Bearings have been replaced on the three short reinforced concrete link-bridges that connect the main pier structure to the berth and pierhead dolphins, and on the upper approach bridge to berth 9.
Working within a strictly limited outage of berth 9 and between frequent sailings on berth 8, the bridges were jacked up to replace the elastomeric bearing pads. The jacks were then removed and the uni-guide bearings were broken out using hydro-demolition and replaced, together with new reinforcement around the bearing pockets.
The design and build contract included installing permanent fibreglass access walkways and ladders below the three link-bridges for future bearing inspection and maintenance. This was previously done with temporary underdeck scaffolding that interrupted ferry operations. At the pierhead link-bridge, part of the 7 m deck was replaced with a fibreglass section containing two access hatches, enabling the walkways to remain clear of the fender compression zones.
Design was by CGR and Tony Gee and partners, and Port of Dover was the NEC project manager and supervisor.
Preferred Contract
The port’s principal engineer Iona Davis, an accredited NEC3 ECC project manager, says NEC is the preferred contract for all Port of Dover design and construction projects. ‘For consistency we have been using NEC3 across all projects and are transitioning all new projects to NEC4. There are a number of NEC4 accredited ECC project managers across the port with further training being rolled out in 2025 to relevant users.’
For the pier F bearings project, Davis says ECC was chosen rather than the Engineering and Construction Short Contract (ECSC) because the works involved sectional completion dates. ‘The project had to align with works occurring in different areas. Our port maintenance team were undertaking an overhaul of berth 9 at the same time, and another contractor was replacing the berth 9 gantry crane.’
She says ECC Option A was chosen because it best aligned with the nature of the work to be carried out. ‘The project was biased towards complex access and installation activities as opposed to material quantities.’
Collaborative working
Davis says the NEC requirement to act in a ‘spirit of mutual trust and co-operation’ ensured the project team worked collaboratively throughout the works, in line with the port’s core values. ‘In practice, close collaboration was achieved through frequent meetings between the contractor, its subcontractors, the port’s maintenance team, the gantry crane replacement team, and the port’s project management and procurement team. These took the form of weekly planning meetings by the relevant project manager, and on the ground as daily site briefings to coordinate the day’s material and equipment movements.’
She says the teams all communicated well, quickly settling into a routine of speaking to and trusting each other. ‘This also involved formal radio communications with Dover Vessel Traffic Service to coordinate the movements of operatives and safety boats to keep berth 8 operational at all times.&rsquo
Davis says other forms of collaboration came in the form of design workshops. ‘For the design of the access walkways, we held design workshops with the project designers, contractor, its walkway designer and the port’s in-house asset inspectors. These workshops ensured the design of the walkways was well coordinated, practical to install, minimised site activities and waste, and would be easy and safe to use by the ultimate end-users.’
Early warnings
She says numerous NEC early warnings were notified by both parties of issues that might impact time and cost. ‘They were encouraged on this project, being seen as good practice to get potential issues out in the open with the earliest opportunity to mitigate them. Many focused on weather conditions, sea and tidal state.’
Davis says a key early warning was the discovery of missing containment reinforcement around the uni-guide bearing pockets. ‘At this stage the project was well underway and there was a risk of delaying the end of the berth 9 outage. NEC-inspired collaboration led to a rapid solution involving readily available reinforcement which could be bent and positioned on site.’
She says compensation events were dealt with fairly and efficiently as laid out in the contract, and the regularly updated programme provided clear visibility on progress. ‘With the help of Asite Adoddle, all NEC notifications, replies and project manager’s instructions were made effectively and within the required timescales, helping to ensure the project was successfully completed on programme and budget.’
The project was shortlisted as finalist for the Retrofit Project of the Year in the 2024 British Construction Industry Awards.
Benefits of using NEC
- An ethos for all parties to act in a ‘spirit of mutual trust and co-operation’ ensured the project team worked collaboratively throughout the works.
- NEC-inspired collaboration extended to working closely with port maintenance and another contractor working on the pier at the same time.
- Early warning process was effectively used as a beneficial tool to proactively manage cost, time and quality issues.