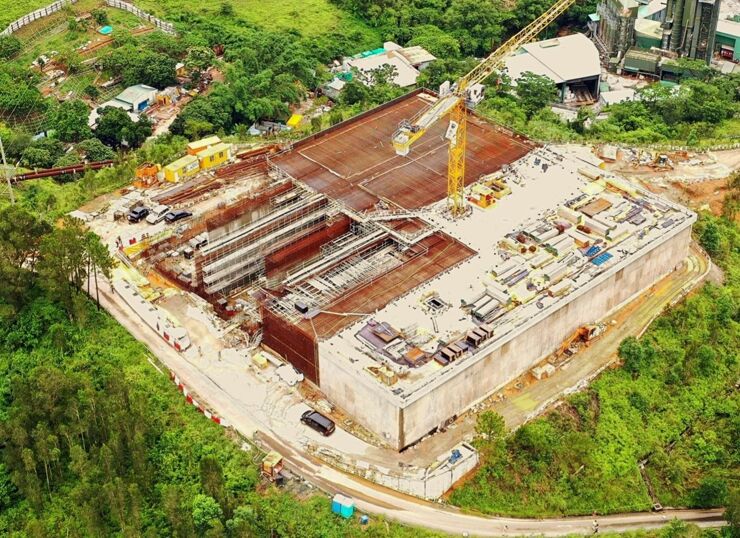
The Hong Kong government is using NEC to improve water supply to the towns of Sheung Shui and Fanling in the New Territories. The HK$521 million (£53 million) project involves building a new service reservoir, equivalent in size to 10 Olympic swimming pools, and laying over 3km of pipes.
Increasing water demand from new housing developments in both Sheung Shui and Fanling made it vital to improve the local supply system to ensure continuing reliability. The new system has also been future-proofed by allowing its conversion from freshwater to seawater or reclaimed water for flushing, enabling the towns to switch to a dual water supply system in line with other parts of Hong Kong when needed.
The project includes a new 24,000m3 low-level service reservoir near the existing high-level freshwater reservoir at Table Hill, Sheung Shui. This new reinforced-concrete storage tank will be fed from the existing Sheung Shui water treatment works by a new 0.6km long, 600mm diameter trunk main, as well as from the existing reservoir by a new 0.8km long, 600mm diameter trunk main.
Water will be supplied from the new reservoir to Sheung Shui and Fanling via a new 1.9km long 800mm diameter distribution main. This will run along Man Kam To Road and Jockey Club Road, and connect with the towns’ existing water distribution network at Tin Ping Road.
The government’s Water Supplies Department (WSD) engaged contractor Vasteam Construction Limited to carry out the works under an NEC3 Engineering and Construction Contract Option D (target contract with bill of quantities) in April 2017. The project is scheduled for completion 3 months ahead of programme and 5% under budget.
Collaborative working
Project manager Irene Pang, chief engineer of WSD’s construction division, says the project team have made a great effort to ensure collaborative working in line with the NEC clause 10 obligation to act “in a spirit of mutual trust and co-operation”.
“To improve cohesiveness and communication, all members of the project team shared a joint site office, wore a site uniform with the same project logo and organised joint charity and sports functions during their leisure time. We also held regular partnering workshops, and these continually revealed a high score in mutual trust within the team.”
She says collaboration on the project was enhanced by extensive use of building information modelling (BIM). “The team worked together on one BIM model and this has resulted in significant time savings on several tasks.”
Examples include offsite pre-fabrication of large reinforcement cages for valve chambers; clash analysis for trenchless construction close to existing raking piles; point-cloud drone surveys for calculating earthworks volumes; point-cloud surveys for checking accuracy of as-built pipework; and using virtual reality animations for safety training.
Prompt problem solving
Following NEC management processes, Pang says the team closely monitored the progress and quality of the works through joint daily progress briefings, enabling any problems to be quickly identified and resolved. “We also sat in on meetings between the contractor and its subcontractors to identify risks and formulate risk-mitigation measures together. Our presence at these meetings facilitated efficient decision making and prompt problem solving, all of which were conducive to good progress.”
She says one unexpected problem that could have caused a considerable delay was the discovery of urns containing human remains during the site formation works. “While we liaised and sought approval from relevant government departments, district councillors and local villages, the contractor re-sequenced the excavation works with four-dimensional BIM to minimise delay. Through joint efforts, the urns were relocated within one month instead of at least a year.”
Unexpectedly high traffic flows along Man Kam To Road and Jockey Club Road were also identified as a potential risk to laying the distribution mains. “Although it was an employer’s design, the contractor strove for the common goal of timely completion and collaborated with us to identify alternative alignments and construction methods for the distribution mains,” says Pang. “This included the adoption of trenchless technology to avoid traffic disruption, shorten the main-laying period and minimise disturbance to nearby egrets during the breeding season.”
Safety and community involvement
In addition to implementing the safety management system required under NEC, the team jointly developed a “Don’t Walk By” culture through which all team members actively identified and reported any unsafe acts or conditions for prompt rectification. So far it has helped to achieve zero accidents.
Representatives of the project manager and contractor have also participated in events with nearby schools, villages and facility operators to help maintain good relationships with them. These events included organising a school fun day, a school drawing competition, bird seminars and an egret-watching tour.
Pang concludes, “Given the strong team spirit developed on this project and through regular reviews of milestone achievements, the project team is confident of completing the works 3 months ahead of the original programme and with a 5% saving on the original budget.”
Benefits of using NEC
- NEC clause 10 obligation to act “in a spirit of mutual trust and co-operation” has helped to ensure strong collaboration between all members the project team, including creating a strong safety culture and developing good community relationships.
- NEC management processes have encouraged close monitoring of construction progress and quality, ensuring early identification and successful mitigation of all project risks.
- NEC collaboration and management processes have directly contributed to enabling the project to be on target for completion 3 months early, 5% under budget and with zero accidents.